Every Beginning is hard
What does a rocket need to launch besides consumables and a place to start? At the beginning of 2022, Project Cryosphere reached the final stages of development for the Liquid Oxygen Hybrid EX-3 rocket. With the rocket nearing completion, it was clear that a full-scale launch test was necessary to validate each component. However, the final requirements were demanding, as the launch site had not yet been determined, and the available options presented vastly different environmental conditions.
The EX-3 rocket architecture, with its passive stabilization, needs to be guided through its initial launch phase. The resulting exit velocity ensures the fin functionality and safe ascend. Therefore, the idea of a big Launch Tower was born, a project of its size never seen in the history of WARR. Over the next one and half years, the Sub Team Cryo-GSE was responsible for working out a working concept. The challenges involved in building something, where experience from past projects is unavailable, required many iterations and new ideas.
Step by Step
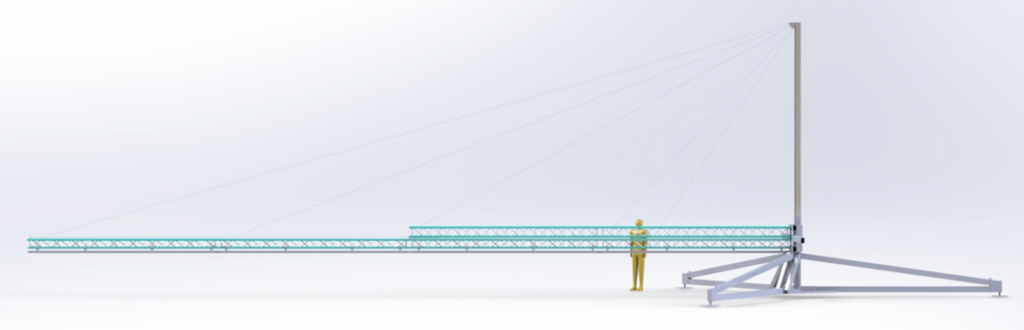
For the first designs, the tower features staggered, commercially available aluminum traverses, which are held by wires attached to a moving back beam. The beam would be pulled down with a commercial rope pulley to raise the whole tower. The guiding rail features a commercial aluminum extrusion profile for attaching the rocket with holding pins. The holding base structure consists of three legs that stabilize the tower. To support the dead weight of the tower, the center piece distributes the load to the ground and only serves to hold the legs in place.
Since every part of the structure has to withstand massive loads while also being as light as possible, problems arise, and small solutions often lead to necessary changes throughout the entire structure. Over months of work, these changes resulted in various designs while maintaining certain requirements and design philosophies.
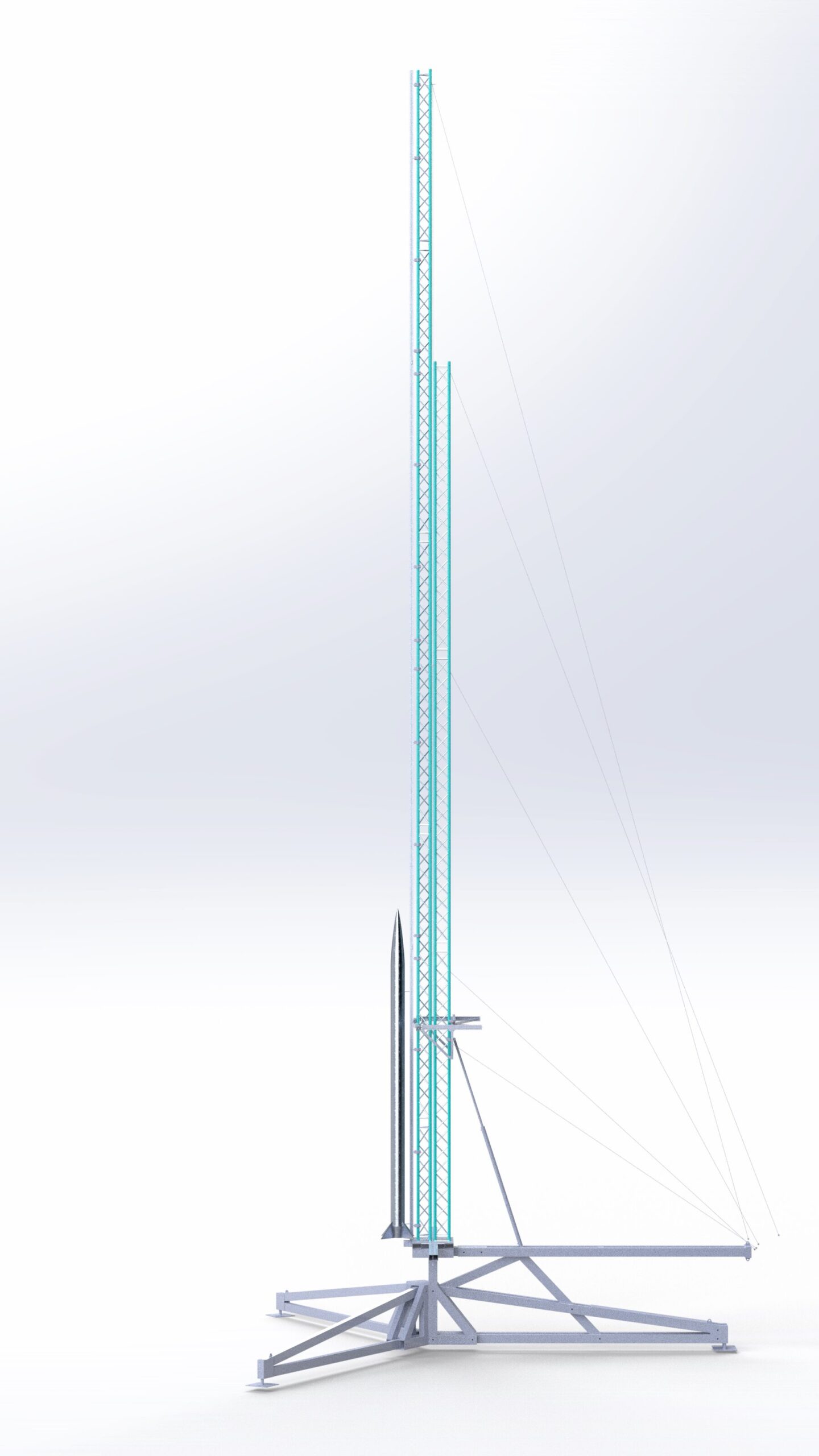
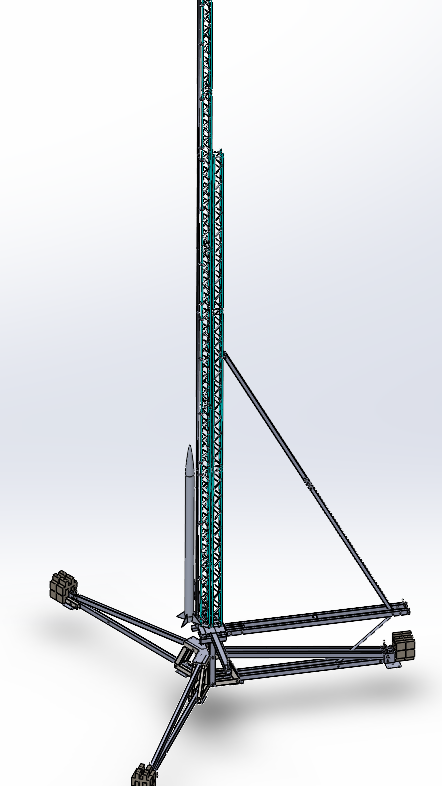

Not the only Way
too Komplex, to many part, truss couldn’t be calculated, structure was not strdie enough, feet would lift up
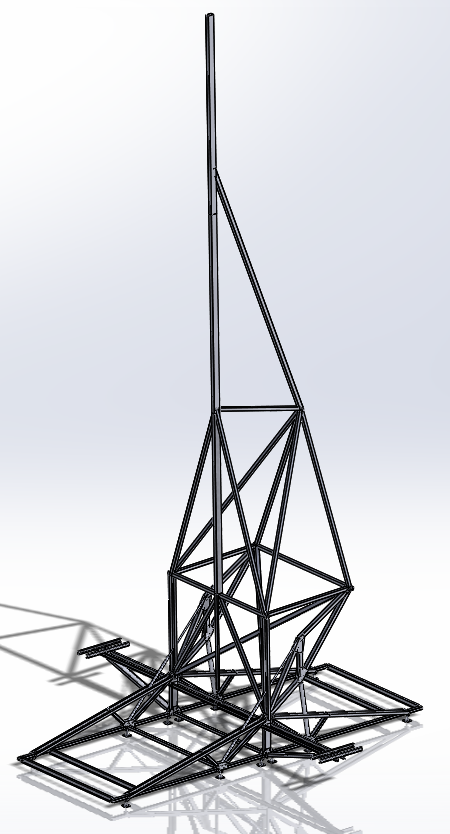

Since the launch site at FAR, California, was chosen and a provided launch tower could be used, the project was canceled. Even though the launch rail now used already exists, a custom-made rail attachment was designed to facilitate simultaneous release and ensure correct tolerances.
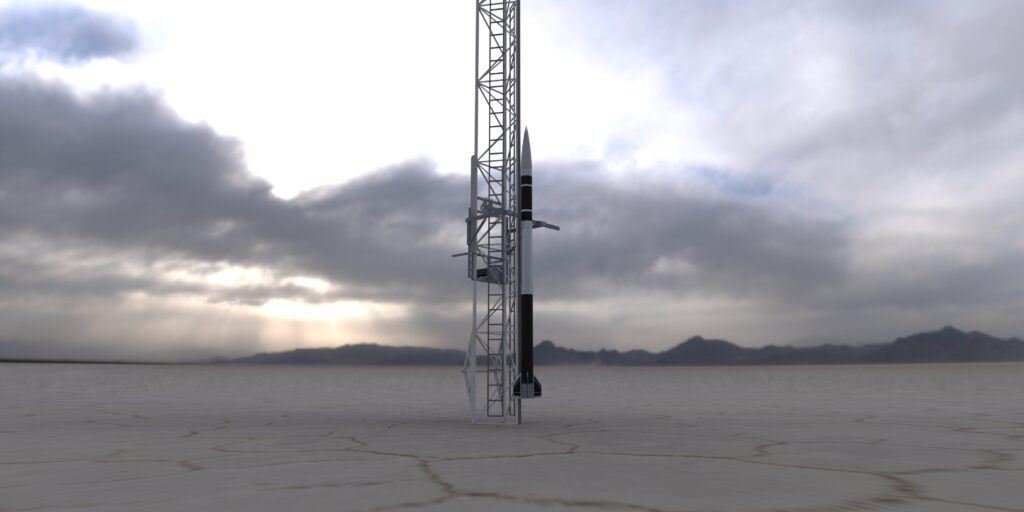
A new Beginning
Since a launch rail was still needed to meet Nixus’s exit velocity requirements, the existing design was revisited and adapted for the new rocket. The vehicle required a longer rail, so the components that had proven effective were repurposed and integrated into an improved system.

How to make it real
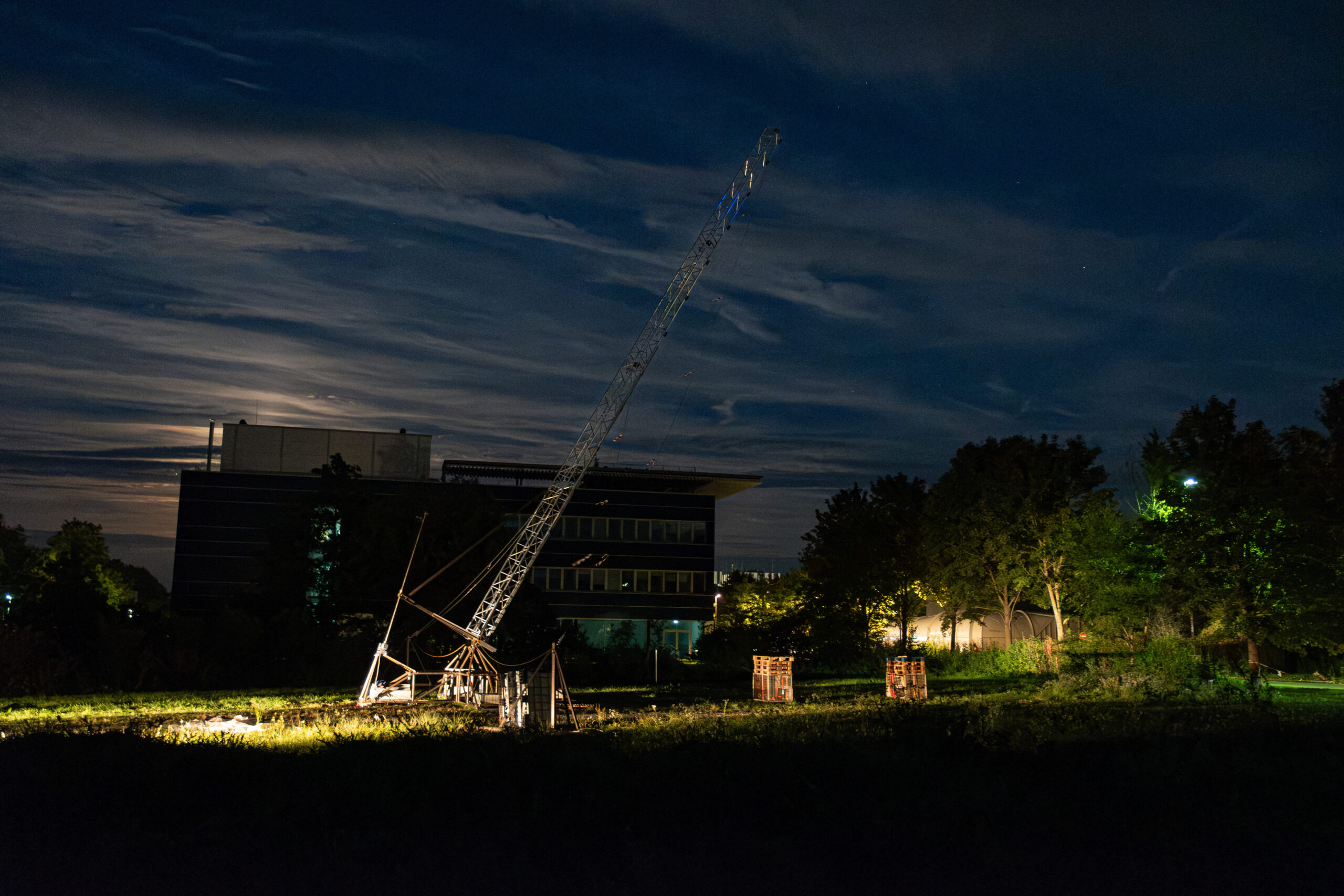